The Futaba Sky Sport Radio has been around for a number of years in various forms and versions. I purchased one in 2005. It always bugged me that opposite the trainer switch was a plastic plug that looked like there should be another switch.
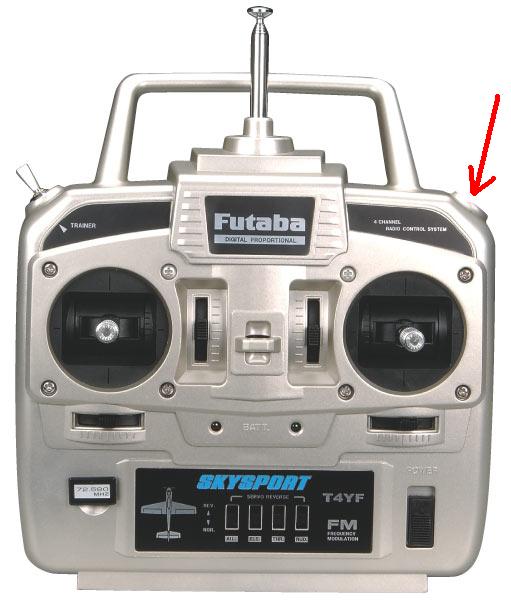
One day out of curiosity, I took it apart and began to study the circuit board. In most radios, there is a multiplexing chip that reads the state of the various inputs and converts it to a PPM serial stream that is fed to the RF unit. The receiver then decodes this pulse train and uses it to signal the individual servos. Following the wires from the joystick pots to where they attached to the board (shown in RED below), and then the traces on the board, I figured out which IC was the multiplexer. (shown in BLUE) After some internet searching and following the other traces feeding into and out of the IC, I found three unused solder pads on the board. (shown in GREEN) Two were 0V and +5V and the third went back to the multiplexer. I thought, "It can't be that simple." I soldered in a 5th pot and wired it to the spare solder pads.
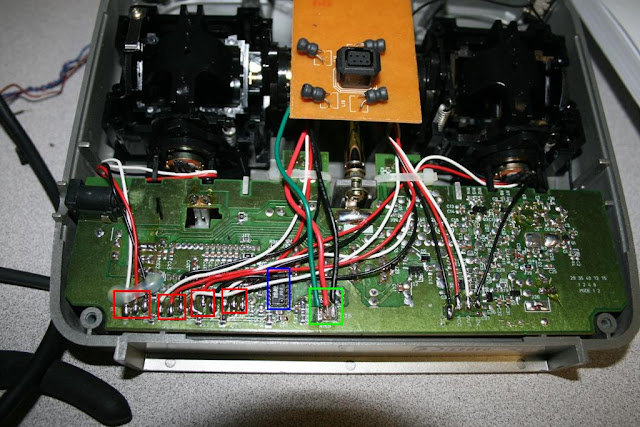
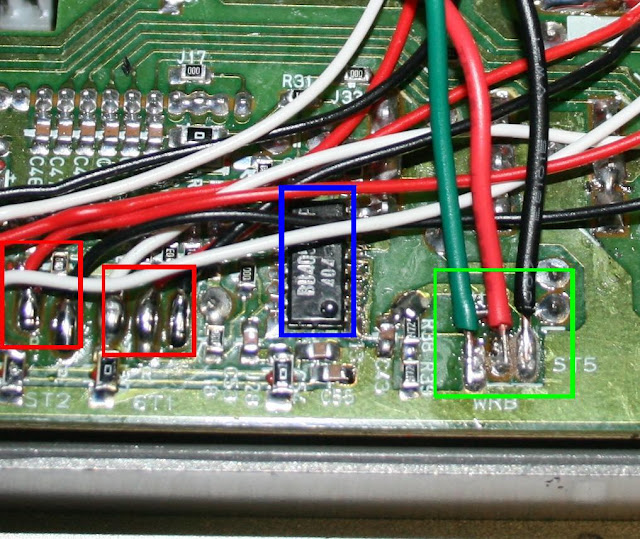
To my surprise it was just that easy! Why the radio was not built this way, I don't know. It even came with a 7-channel receiver and I am not a aware of a factory 5 channel version that would have been built on the same framework.
A friend of mine, who makes jewelry, recently laid down a challenge for me to create something "crafty". Being an engineer, I am anything but artsy, but I gave it some thought and after a few hours playing on the mill I came up with this:
It was suppose to be tiny wheel, but my first attempt did not turn out so well. As you can likely see from the photo above, while doing the various machining ops, I lost my zero on the DRO and when I went to drill the center bore and lug hole pattern, they were off center. In addtion, the center bore was too big and the lug pattern ran into it due to the flex in the drill bit I was using. So I punched out the whole center and chocked it up to a learning experience.
Discourage my mill lost its zero and knowing that I could not sleep well without figuring out why, I headed back to the garage around 10:00pm. It didn't take long to conclude that the likely culpirt was a loose gib on the X-axis. (The Y maintains a perfect zero.) After some adjustment, I was up and running again. Now encourage, I pressed forward with a second attempt at producing a miniature wheel. This time I drilled the lug holes first using a center drill to lay out the pattern followed by drilling the hub bore after double checking that I was still on center. This worked much better aside from the 1/16" bit snapping off in one of the holes.
My second attempt still needs polishing, but it turned out much better than the original and makes a cool desk trinket. I was even able to punch out the broken drill bit after milling the backside counterbore.
Update 1/28/13: I finished a few more to hand out to some friends and one made from aluminum which turned out nice.
In my never-ending quest to expand what I can fabricate, I purchased a set of SPC / Light Racing flared hole dies. I got a good price on these and as a bonus, they are also highly engineered, using Finite Element Analysis to optimize the angle and radius of the die in order to achieve the maximum depth of flare without cracking the base material.
My first experiment was with a very thin piece of aluminum sheet I had laying around. I cut holes in it for all 5 sizes of dies I purchased and used a hydraulic shop press to create the flares.
There's not much to it, but these are great for adding bending and compressive strength to sheet metal pieces.
My other tool is a battery lug crimper I made for an upcoming solar project. (More on that later!) This was a quick test to see if it was possible to achieve a good crimp with minimal time invested.
Sadly this worked, but not as well as I hoped. The lug is crimped tightly, but the tool cuts into the lug if clamped too hard. I will try again later when I have more time.
And finally, I received a new Ham radio for Christmas with APRS capability!! (A Yaesu FTM-350ar to be exact.) But the suction cup mount that came with the head unit absolutely sucks. It's so bad they give you an adhesive doughnut to stick to your dash because the suction cup can't stick to anything on its own. Well this just was not going to cut it, so I whipped out a bracket to mount the head unit to the dash via the un-used ash tray.
I'm not sure if I'll leave it here permanently, but it works well and it is easy to push the buttons with my fore finger while shifting gears.
I purchased an '02 DR-Z400S (with Kawasaki skins) in March of 2011 for exploring trails around Colorado and Utah. The bike appeared mechanically sound, but was a little rough around the edges. I spent most of the summer fixing little things and making upgrades to improve reliability. One of the previous owners had re-routed the ignition wiring in order to run the bike with no lights. (Don't ask me why.) On the bike's first trip to Moab, I dumped it within 2 hours and killed the factory speedo. It was replaced with a nice Trail Tech Vapor unit and gave me an opportunity to fix the wiring harness and return it to stock. I was even able to wire the Vapor to work with the factory plugs.
But I digress...
Fast forward to Spring 2012, I was using the bike to commute to work and racking up the mileage. The engine was using a fair bit of oil between changes and I decided to rebuild it before the summer riding season. After doing some research, it was soon discovered that increasing the displacement would not cost much more than a standard rebuild. Lucky for me Eddie Sisneros, the guru of DRZs, had just moved his shop and was now on my way home from work. Eddie is a great guy and offered up plenty of advice from parts to procedures. Although I have rebuilt plenty of car engines, high performance bike engines have some special considerations and I was concerned about doing this right the first time.
I settled on a 435 big bore kit. This allowed me to fix the oil burning problem and up the displacement without splitting the cases. Limiting myself a 435 (94 mm piston) avoided some of the problems of the larger bore kits. Here she is going under the knife and a pile of shiny new parts:
After removing all the plastic and the fuel system, I carefully removed the cams and the head. The piston was next. Here is the old next to the new. The over fueling and burned oil is easy to see. The new piston has lots of extra material removed, I assume to keep the weights similar, although I never check for sure.
With the piston removed, I checked the bore on the wrist pin bearing and the play in the crank bearing. To my relief, both were well within spec, which meant I didn't have to split the case to replace the connecting rod bearings. Besides the larger piston, the kit came with a new cylinder jug. Boring these cylinders is not as easy as a car engine, as they are Nickel Carbide coated over aluminum instead of plain cast iron. To bore them requires re-plating and frankly that is not worth it when a new replacement is relatively inexpensive.
In addition to the big bore kit, the timing chain was at the end of its life and in need of replacement. As you can see, the chain is trapped by the clutch basket.
After removing the clutch basket, the chain was slipped off and I used the opportunity to Loc Tite the left-handed nut on the crank, which is well known for coming loose.
The previous owner had tore up/seized up the access plug to the flywheel nut. I was able to score a new one for free, but the old one was not coming out peacefully. After fighting with it for an hour and getting nowhere, I gave up and pulled the stator cover. Modifying a tool a had for a Dana 44 axle ball joint and using an impact wrench, I was able to remove the inspection plug without damage to the case cover.
In the process however I lost a small bushing for the starter counter shaft. After some reading I discovered that this is a common problem when removing the stator case cover. Oh well, lesson learned. I was able to fabricate a new bronze bushing and continue my work after checking to make sure the wayward bushing had not fallen into the engine.
On Eddie's recommendation, I had him rebuild the head with stainless one-piece valves. One of the more documented problems with the DRZs is the factory 2-piece valves separating and taking out the upper end. On any other day I would have done this job myself, but I was under the gun to get the bike back together and the tooling and parts would have cost more than having Eddie do it.
With the head done, I could start putting the engine back together. The first step was installing the new timing chain and clutch basket. Followed by the new piston and cylinder.
Since I use the bike to travel to remote places where premium fuel is not always available, I decided to stick with the stock compression ratio and therefore be able to burn low octane gasoline. With this kit it is possible to raise the compression ratio by using only one layer of cylinder gaskets instead of three. S-models have slightly lower compression than their E-model counterparts allowing them to run on low octane fuel at the cost of a few horsepower.
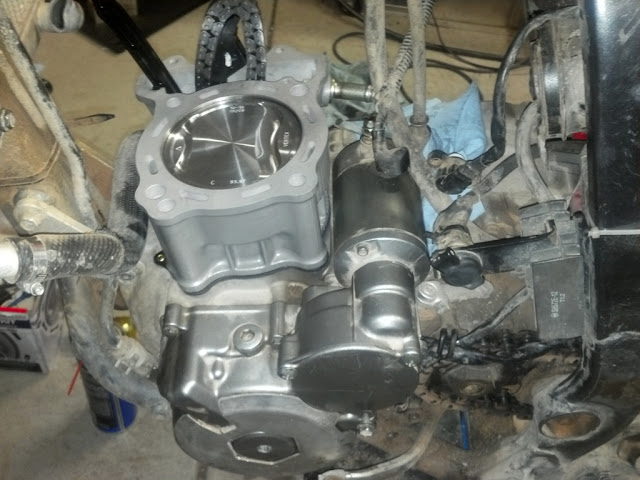
Installing the head and fuel system went smoothly. Special attention must be paid getting the cams timed properly, but taking my time, this was not a difficult task. The bike fired up immediately and no idle adjustment was necessary to compensate for the larger bore. There are many schools of thought when it comes to breaking in the engine. I followed the kit's instructions and kept it under half throttle and 6000 rpm for 500 miles. ( I think it was 500, but I honestly don't remember. ) Afterwards I changed the oil and filter, checked all the bolts and took it out for a spin. The kit really improved the low end torque, which works great with my 15/44 gearing. Top end HP feels about the same, but I suspect that the smaller S-model carb limits the top end HP. A head to head drag race with my friend's lighter and more aggressively geared DRZ400E proved that the big bore really did make a difference. Despite the E-model's higher compression and bigger carb, my bike was able to pull out a noticeable lead in a 1/4 mile and by then the "E" was top out and I still had plenty of RPM left in reserve thanks to my more street friendly gearing.
On the trail, the extra displacement translated to better out-of-the-hole performance. Great for low speed maneuvering in the rocks. The first trip out ended up being a 400 mile/2-day over-nighter around northern Colorado with a co-worker and his XR400. The trip was about 80% dirt and trails. The first day alone, I logged 17 hours of saddle time and it was a great shake down for the bike. ( I had it loaded with 175lbs of rider and 50+lbs of gear. )
After getting the bike home and cleaned, I inspected it again for leaks and loose bolts. To my surprise nothing had come loose. I really expected at least one loose bolt. Overall, I'm happy with how the bike turned out, especially since it burns zero oil now. I can't wait for warmer weather to return!